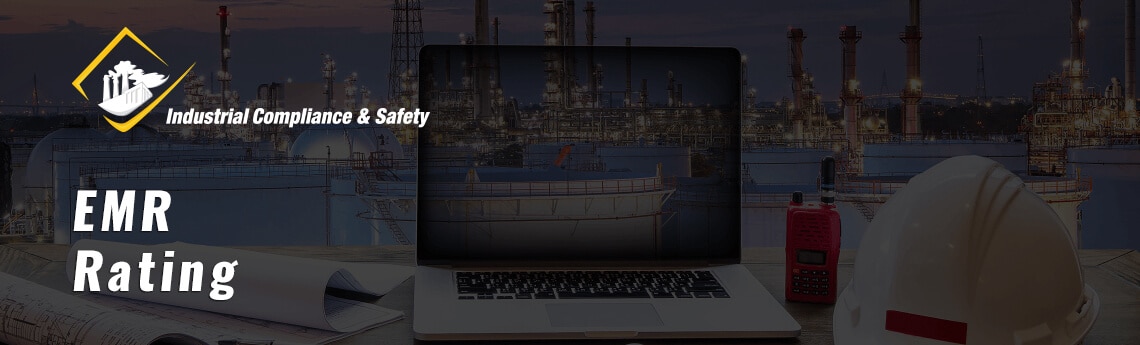
Experience Modification Rating
Experience modification ratings also called EMRs are used by insurance companies to price workers’ compensation premiums. Having a good EMR score can help keep your insurance premiums low and give you the competitive advantage.
What is an EMR?
Worker’s compensation is a payout that occurs after an on-the-job injury. By looking at your company’s EMR rating, an insurance company can assess the cost of past incidents and gauge future risks. You can think of an EMR rating like a credit score, as it draws data from your company history in order to predict future liability.
EMRs also help your company stand out when competing for work out in the field. A lower EMR suggests you are a low risk, compliant company to hire. When competing for a potential job, having the lower EMR rating may be what wins your company the job.
How EMRs are Calculated
EMRs are calculated by advisory organizations, the most common of which is the NCCI (National National Council on Compensation Insurance). In fact, the NCCI developed the formula for calculating EMRs. This formula considers your company size, history of workplace injury over a three-year average, and the rate of incident for other companies in your industry.
For every industry, the average EMR is 1. If you have a rating higher than 1, then you have a higher than average rate of injury and you will be charged a higher workers’ compensation insurance premium. If you have a rating lower than 1, then you have a lower than average rate of injury and you will be charged a lower workers’ compensation insurance premium. Newer businesses that have less than 3 years of claims to be reviewed usually have an EMR calculated at 1.0.
Ways to Lower Your EMR
Two of the main factors that affect your company EMR rating are the type of incident ( cost to insurance) and payroll size. You can lower your EMR by investing in a robust safety program. Educating your employees and encouraging proactive activities that help avoid accidents over time can help reduce incidents and in the long run lower your EMR rating.
How to Obtain Your EMR
If your company has already been experience rated, then you can contact your insurance agent for a copy of your current EMR Letter.
If you are not familiar with EMRs then chances are you have not been rated yet. In order to be rated for your EMR, you will need to reach out to your Advisory Organization. Advisory Organizations can vary from state to state. The NCCI is the most popular Advisory Organization, as it provides services to 33 states. If your company is in California, Delaware, Indiana, Maryland, Massachusetts, Michigan, Minnesota, New Jersey, New York, North Carolina, North Dakota, Ohio, Pennsylvania, Texas, Washington State, Wisconsin, or Wyoming, you will need to file directly through a state-specific insurance rating organization. After contacting the appropriate Advisory Organization, you will be asked to submit your company information and OSHA logs before receiving your company EMR.
There are a few scenarios where a company will not qualify for an EMR. Some companies cannot be experience rated because they are too small. Other companies do not qualify for an EMR because their premium is too low. In these cases, you will not be able to find your rating because EMRs do not apply to your company.
Industrial Compliance & Safety can help your company with the process of obtaining their EMR rating.